More and more
enterprise are transforming their shop floor from machine to machine
into connected dots to best prepare themselves for the needs from the
ever-changing business realm - faster response, flexibility and
customization.
By monitoring the
status of equipment and WIP (Work in Process), it ensures a smoother
production process and reduce machine downtime. Furthermore, it shortens
the production lead time thus enterprises can have a faster respond to
the market in a timely, more flexible and customized perspective.
Successful Cases that Inspire
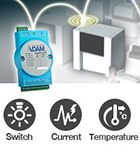
Plant Equipment Monitoring and Optimization
Often the machine status takes various sensor to monitor, and the shop
floor of the plant are fully equipped with a thorough layout design
which makes the revamp planning a complicated task. Advantech ADAM
modules are suitable for various application based on sensor and
networking specification requirements.
Work in Process Monitoring
To optimize the production process, also to ensure the quality of the
product, the product line needs to be monitored systematically typically
with a internal Manufacturing Execution System. For well control the
storage environment quality and ensure the product information to be
precise, the robust design and a 23-year-reliability of ADAM I/O module
makes it the ideal choice for data acquisition